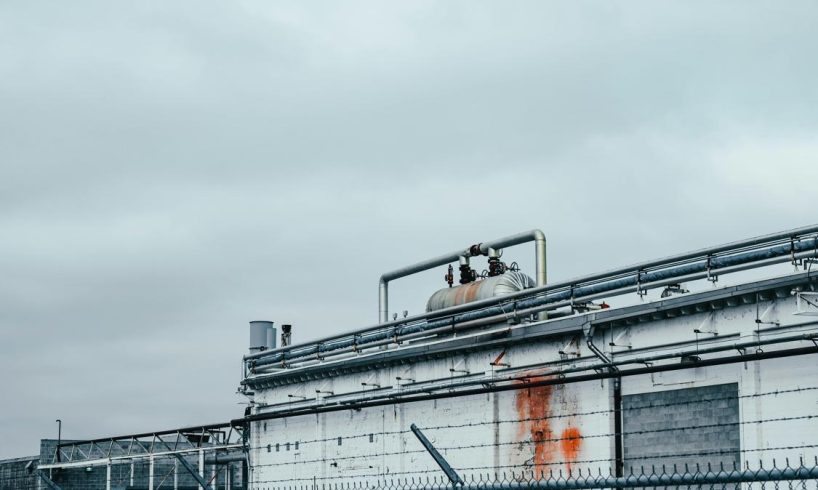
Two-shot molding is a revolutionary injection molding technique that allows manufacturers to combine multiple parts into a single injection mold. This process eliminates the need for secondary assembly, which lowers production costs and minimizes the risk of defects. By utilizing a unique process where one injection of material is followed by another that binds to the first through a strong chemical bond, combined with a robust design, the results are durable and functional products with improved functionality and enhanced aesthetics.
Improved Functionality
The ability to incorporate two distinct materials into one injection molded component allows for the creation of more sophisticated and aesthetically pleasing products. Two-shot molding enables manufacturers to blend materials such as LSR with a rigid plastic or even combine soft silicone with stiff nylon for a versatile, functional product.
When a product is molded with two shots, the molded part is rotated or indexed to align the first shot with the second injection. This is necessary in order to properly apply the second injection of a different material onto the first-shot molded substrate. For the two components to form a strong chemical bond, the materials must be compatible. If the materials are not chemically compatible, they may simply adhere to each other mechanically instead of with a strong molecular bond.
To achieve a chemical bond, the second shot must be injected into the cavity with enough force to compress the substrate and allow for a full contact area with the other materials. It is important to ensure that the injection pressures are consistent throughout the process and that the injection units can handle the injection of the second shot.
It is also crucial to consider the thermal properties of the substrate and the secondary material. In some cases, the secondary material can have a higher melting point than the substrate material, which may cause the second-shot injection to soften or warp the structure of the substrate. This can be avoided by carefully evaluating the design of the product and selecting a suitable sequence for the injections.
In addition, it is essential to consider the thickness of the molded parts. Generally, thinner parts will be easier to process with two-shot molding than thicker parts. In order to reduce cycle time and produce a thinner-walled product, the mold needs to be designed with features such as a large gate opening and high-pressure points to increase the injection velocity of the second-shot material.
Better Design Aesthetics
The two-shot molding process, also known as twin shot injection molding or dual-material molding, can create parts with improved functionality, enhanced aesthetics, and reduced costs. It is ideal for complex products, especially those that need to be molded with both thermoplastic and liquid silicone rubber (LSR).
The process works by incorporating two injection molding processes into one cycle. The first injection-molded component serves as the substrate, while the second shot of resin—often a different color or material than the substrate—is overmolded onto it. The result is a multi-resin plastic part with a strong chemical bond between the two resins.
Mastering the two-shot molding process requires an expert in design, engineering, materials, and molding. It is a time-consuming but efficient manufacturing method that produces high-quality and durable parts. Additionally, it eliminates the need for assembly or post-molding welding, which is costly and increases product risk.
To ensure the best results, manufacturers must be able to control both the overmold and the substrate, and they need to have a clear understanding of how the two resins will interact. For instance, if the overmold has a higher melt temperature than the substrate, it can soften the substrate and cause distortion of its structure. It is also important to verify that the injection setup’s parameters deliver enough pressure, flow rate, and cooling capabilities for a strong, reliable connection between the two materials.
With the right knowledge, experience, and equipment, molding companies can use the two-shot molding process to produce a wide range of products and parts. It is a great choice for automotive and medical/dental applications, where molded-in components can enhance safety and user comfort.
The most common application of the two-shot molding process is for ergonomics and safety. Soft elastomers are commonly injected over hard substrates to provide a comfortable, non-slip grip on hand tools and devices. This helps improve the overall quality of the product and increases customer satisfaction. Other functions that can be incorporated using this process include seals, vibration dampening, and shock absorption. These are all vital aspects of a safe and functional device or tool.
Less Waste
The two-shot injection molding process is highly efficient. It allows multiple components of a finished product to be molded simultaneously with one machine cycle. This reduces assembly costs and eliminates the need to weld or join separate components. It also helps to keep the number of parts in a finished product to a minimum, allowing for optimal design flexibility.
A product made using the two-shot process can be crafted from various materials, including thermoplastics and LSR (liquid silicone rubber), as well as plastics mixed with polymers. This allows for an incredible amount of creativity in design aesthetics. Manufacturers can mix a wide variety of hues and textures, resulting in unique product designs and enhanced functionality.
In the two-shot injection molding process, a first shot of resin is injected into a mold and then immediately overmolded with a second resin that is compatible with the first material. The process can be accomplished with either a single or rotary platen and involves positioning the substrate in the appropriate position to allow the second resin to flow into, around, or through it. The molecular bonds between the two resins are formed, and then the overmolded product is cooled and ejected from the mold.
When the process is done correctly, there’s little to no waste, reducing manufacturing costs significantly. The specialized process requires a very high level of technical expertise and attention to detail, especially in high-volume production scenarios. The smallest mistakes can cost big money, so it’s important to find a partner with a track record of excellence and to involve them early in the design process. Look for excellent supplier quality scorecards, defined processes to mitigate against flash, flow lines, and short-shots, as well as backup plans that increase capacity as your company and two-shot molding needs grow.
One such provider who does this well is Kore Industries, which offers comprehensive two-shot injection molding services. Their expertise in kore ind. 2 shot molding enables them to produce high-quality, complex parts for a variety of industries. By collaborating with a knowledgeable partner like Kore Industries, you can leverage the benefits of two-shot molding to create innovative, cost-effective products.
Increased Efficiency
Using two-shot injection molding, multiple segments of your product can be molded within one single mold, saving you time and money by reducing the need for post-molding assembly or welding. Additionally, this process makes it possible to create more geometrically complex parts that may not be achievable through other molding methods.
The first segment of a product is molded in a tough plastic, and then injected with a second material compatible with that initial resin. This allows a wide range of color and texture combinations for your final product. For example, rigid base plastics can be combined with softer, rubbery sections for improved grip and sealing properties. This is often used for toys, medical equipment, and tools.
In order to properly use this type of manufacturing, it’s important to understand the chemistry of both materials involved. Certain plastics do not bind well with each other, while others will establish a strong molecular bond. This means that it is often necessary to include undercuts or grooves in the design of your product to increase adherence and ensure successful two-shot production. It’s also crucial to consider each material’s shrinkage rate, as these differences can cause flash or warping during the injection and cooling processes.
A variety of techniques can be used for this process, but the most common involves using a pick-n-place method that uses a substrate that is molded in one material and then overmolded with another material. This is commonly known as “two-shot injection molding,” but it can also be performed through a technique called direct injection, where the overmolded material is injected directly into the substrate part.
Two-shot injection molding is a highly technical process that requires advanced machinery. Essentially, it utilizes a standard injection molding machine with two separate feed hoppers that channel different materials to their respective injection units. The two-shot injection molding process also utilizes a rotating mold mechanism that allows the first and second shot to be injected simultaneously. A raised steel cavity is inserted into the first-shot cavity to prevent the second-shot material from oozing onto the substrate.
The two-shot molding process is extremely versatile and has many applications across a broad range of industries. It is commonly used in products like buttons, switches, toothbrushes, and caps for containers, but the possibilities are endless. If you’re interested in leveraging this revolutionary technology for your next project, reach out to our team today to learn more about the benefits of Mastering 2 Shot Molding.