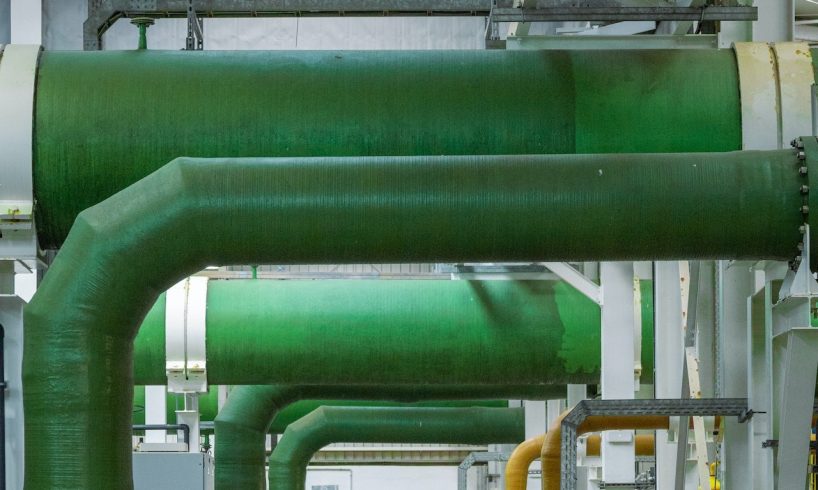
Poor construction quality can be one of the primary contributors to subsurface drainage project failure, so any actions taken to enhance construction quality must also aim at increasing system durability. There are various measures available for improving this aspect.
Substandard pipe and fitting materials entering the supply chain is of great concern, leading to hydrostatic test failures and excessive pipeline expansions.
Inspection
Plumbing professionals often perform inspections of pipelines as part of their drain maintenance work on residential properties, in order to detect and fix potential problems before they become costly issues. Furthermore, plumbers will need to test for leaks using techniques like bag testing or water pressure testing in addition to inspecting.
One method is using a CCTV inspection camera. This powerful tool can quickly identify even small cracks, dent, or holes in pipes – especially helpful when monitoring sewer systems where visual inspection can be difficult and where leakage or breaks may have taken place. Furthermore, this method identifies leakages or breaks more effectively.
One effective and affordable method to detect leaks is smoke testing, which involves blowing smoke into pipes to see if any gaps or cracks in them allow escape of its smoke through gaps or cracks in drains. This technique provides a straightforward way to find any potential issues within drain lines, whether that is through leaks or cracks in their construction.
This type of inspection should be carried out by a trained technician who is certified in operating and interpreting equipment and results. A written report may also be generated which helps pinpoint any potential issues with drainage system operation.
The NASSCO PACP standard is widely utilized across North America to evaluate the internal condition of sewer pipes and prioritize maintenance and rehabilitation interventions. Engineers, managers and finance departments rely on this data to prioritize maintenance and rehabilitation interventions; engineers often rely on its results when making maintenance and rehabilitation decisions.
According to this standard, PACP data must be recorded and coded consistently; however there have been variations among software programs in terms of how PACP data are coded – this research quantified their impact on database quality for the first time as well as tools that industry stakeholders could utilize in improving it further.
Testing
Quality pipeline drainage systems are vital for safe and reliable operation, meeting specific governmental and industry safety standards to avoid leaks, fires, or explosions. To do this safely and reliably requires performing non-destructive testing on pipe conditions as well as inspecting welds and dimensions – as well as evaluating workmanship quality to make sure pipes made with top-grade materials.
Sampling is the cornerstone of quality control for any product, as any test conducted on any given sample must accurately represent all batches produced by that particular batch of product. Sampling requires trained team of personnel who understand safety precautions to conduct this procedure effectively.
Quality control programs must also be established at factories producing pipes. These programs should include inspecting all components that go into making the final product as well as recording and reporting data in order to detect any potential defects that arise during production. This will enable timely identification of any potential issues or defects during the process.
Manufacturing plants follow three stages of inspection and testing: (i) receiving material inspection; (ii) in-process material inspection; and (iii) outgoing/final product testing of finished product.
At each of these three steps, quality control personnel examine materials that will be used during manufacturing to check that they comply with any specifications in a purchase order or contract, inspect for damage such as corrosion or cracks, and also look out for potential issues like these during receiving inspections.
Quality control plans in sewer drainage construction are integral for avoiding issues during construction. A plan should include all steps required to create a comprehensive inspection and maintenance record, analysis of survey results to identify areas for improvements, list of required maintenance tasks with their schedules as well as include an outline of all stakeholders involved with the project responsibilities and duties.
Maintenance
Maintaining and repairing pipeline drainage systems are an integral component of their proper function, not only saving money by avoiding expensive damage to buildings and structures but also protecting human lives and the environment from degradation.
Regular inspections of your pipe system can detect issues before they become more serious; in addition, having an effective drainage system in place will help mitigate storm impact on roads and bridges as well as lower contamination risks in water supplies.
There are various means available to maintain and repair pipelines, such as visual and mechanical inspection. Visual inspection entails visually inspecting for corrosion, leaks, or any signs of wear; mechanical inspection uses special tools to assess quality work performed and pipe dimensions; depending on their results, pipelines can either be cleaned up or rerouted depending on results of tests conducted on them.
Maintenance and repair of pipeline drainage systems often requires significant investments, which is why selecting an experienced contractor with access to various tools and equipment necessary for successful projects can save both money and hassle. To minimize such projects, choose an organization with expertise in this area – this way any costly projects can be avoided quickly and cost effectively.
PHMSA believes the voluntary industry technical standards it incorporates into its PSRs provide pipeline operators with opportunities to take advantage of improved technologies, new materials, performance-based approaches, manufacturing processes and lessons learned from pipeline incidents – thus helping ensure hazardous liquids and natural gas reach their destinations safely.
Reconfiguring existing voluntary practices to mandatory standards can also help decrease the chance of accidental product release, including replacing “should” with “shall.” For instance, this change could occur with regards to an existing requirement such as outdoor storage resistance testing.
Cost is often a primary consideration for pipeline owners when it comes to maintaining or repairing their pipelines, so trenchless solutions offer an alternative means of doing this work without extensive excavation work or excavation costs.
Hydraulic cleaning systems and thermal water jets are among several such technologies used for trenchless solutions that help clean clogged pipes or restore damaged sections, while another approach includes inserting an in-place liner that heats and seals around existing pipework – methods which may reduce excavation requirements while cutting costs associated with such projects.
Repair
As part of a common practice to monitor the condition of sewer pipes, PACP data (pipeline characterization and condition) are increasingly utilized as a monitoring tool. This data assists system owners, managers, finance departments in prioritizing maintenance interventions as well as rehabilitation measures. To ensure PACP data are accurate and consistent with each other, it is imperative to define appropriate quality metrics to measure this information.
This proposed NPRM is tailored to achieve exactly that goal. It outlines a methodology for the creation of quality evaluation metrics, with particular attention paid to data collection, storage, manipulation, reporting and infrastructure needs. Furthermore, the proposal describes how these metrics will support performance-based pipeline maintenance practices.
PHMSA incorporates voluntary consensus industry technical standards into its regulations via reference every two to five years, updated by various international and domestic standard development organizations (SDOs).
These organizations utilize established procedures for review and revision that allow them to identify new technologies, materials, or management practices which may improve physical integrity or operation safety of pipeline facilities. Swiftly unblock drains with our professional services.
PHMSA regularly evaluates updated industry standards to determine whether they meet its regulatory objectives for inclusion in its PSRs. Doing so helps avoid confusion and expense associated with having to adhere to multiple versions of an industry standard, and allows operators to focus their resources more directly on meeting compliance regulations at their facilities.
Though this NPRM proposes to include by reference revised editions of industry standards containing editorial and clarifying changes, none should result in substantial compliance costs for operators due to voluntary adoption by most pipeline operators and seamless incorporation into current operations and maintenance activities.
Integrating updated standards would also assist PHMSA in avoiding conflicts between its regulations and more recent versions of standards that the majority of industry applies voluntarily in daily business practices, thus eliminating duplication of effort and resources within industry and freeing more energy to be put toward ensuring hazardous liquids and natural gas reach their destinations safely and securely.